|
Plus d'informations sur les produits VISI-Flow : www.vero-software.fr
La Rhéologie
Strictement, la Rhéologie est la science qui étudie l'écoulement
et la déformation des matériaux, que ce soit à l'état solide (élasticité)
ou à l'état liquide (viscosité). Dans l'esprit du plasturgiste,
il s'agit de l'étude de l'écoulement du polymère fondu dans le
moule.
On appelle aujourd'hui logiciels de rhéologie, l'ensemble des
logiciels de calcul permettant de simuler le comportement du plastique
à l'intérieur du moule. Il serait plus exact de parler de logiciels
de simulation de l'injection.
Ces différents logiciels, qui au début (1980-85), se cantonnaient
au remplissage de l'empreinte, permettent aujourd'hui de simuler
le comportement du plastique pendant la phase de maintien en pression
(compactage), pendant le refroidissement de la pièce (thermique),
et après démoulage de la pièce (déformations).
Les différentes variantes de l'injection peuvent également être
simulées : injection de gaz, injection séquentielle,
injection multi-matière, ...
Intérêt de la Simulation
La simulation de l'injection s'inscrit parfaitement dans la politique
de réduction des coûts et des délais de développement rencontrée
chez la plupart des donneurs d'ordres. L'intérêt est de prévoir
par le calcul des défauts qui pourraient apparaître sur les pièces,
et de trouver des solutions avant que le moule soit réalisé.
Les solutions peuvent se trouver aussi bien au niveau du dessin
de la pièce que de la conception du moule.
Traditionnellement, ces problèmes sont découverts lors des premiers
essais de l'outillage, et leur résolution passe des modifications
d'outillages. Souvent des moules d'essais sont utilisés pour tester
certaines solutions. Les coûts générés sont très importants :
immobilisation de presse pour essais, consommation de matière,
heures de techniciens, démontages et remontages d'outillages,
heures d'usinages, coût de transport, ... sans compter les dépassements
de délais difficilement chiffrables.
Comparativement, les quelques heures passées à simuler ces essais
à l'aide d'un ordinateur sont très vite amorties. Il est souvent
possible de supprimer le moule d'essai et de lancer directement
le moule série. L'intérêt pour le donneur d'ordre ou le transformateur
est d'intégrer la simulation le plus en amont possible lors du
développement d'un produit.
Les Logiciels
Ces logiciels ne sont pas des "systèmes experts" et
une part importante du travail réside dans l'interprétation des
résultats de calcul, pour trouver des solutions d'amélioration.
Les différents logiciels peuvent être classés en trois grandes
familles, en fonction de la méthode utilisée pour représenter
la pièce à étudier :
Outils d'évaluation
Avant de simuler complètement le process, il existe des
outils permettant de "dégrossir" le travail et
d'évaluer le moulage de la pièce : Outils
d'évaluation
Logiciels "2D"
Utilisée au tout début de la simulation, cette
technique n'est plus utilisée aujourd'hui. Avec ces logiciels
dits "2D", la pièce et les canaux d'alimentation à étudier
étaient découpés en segments de forme simple (cylindres,
plaques) correspondant approximativement à l'écoulement de la
matière dans le moule. Cette méthode était bien adaptée
à l'étude de pièces de formes simples (seaux, pots, boites, bouchons,
...), et surtout au calcul des systèmes d'alimentation : carottes
froides, canaux chauds, canaux isolés. Dans le cas d'étude du
système d'alimentation uniquement, la pièce peut être remplacée
par une plaque de volume équivalent simulant le débit de matière
traversant les canaux.
Avantages : étude très rapide, simplicité de
construction du modèle, rapidité des calculs (quelques secondes),
changement des conditions d'injection ou des épaisseurs rapides,
modélisation facile du système d'alimentation
Inconvénients : la modélisation de pièces complexes
est délicate, chaque déplacement du point d'injection nécessite
de refaire le modèle, calculs limités au remplissage.
Logiciels surfaciques, appelés
aussi 2.5D. Simulation fibre neutre
Ces logiciels utilisent des "éléments finis" de type
"coque". Dans ce cas le maillage représente une "peau"
de la pièce, l'épaisseur n'est pas représentée à l'écran,
mais est définie comme une propriété de chaque élément. On parle
aussi de maillage de "fibre neutre". Cette méthode est
bien adaptée à l'étude de pièces, dans lesquelles l'épaisseur
est faible devant les autres dimensions. Il est facile d'essayer
plusieurs configurations de points d'injection et de voir la position
des lignes de soudure. Les résultats visualisés sous forme de
cartes en couleur sont assez parlant.
Les résultats, disponibles sous formes de cartes en couleurs
et graphiques, indiquent l'évolution de paramètres tels que la
position des fronts de matière, la pression en tout point du moule,
la température matière, les contraintes et taux de cisaillement,
l'épaisseur de gaine solide, l'orientation des flux de matière,
...
Avantages : changement facile de la position et du nombre
de points d'injection, modifications aisées de la géométrie
de la pièce. Simulation du process complet d'injection (compactage,
thermique, déformations). Calculs rapides (quelques dizaines
de minutes).
Inconvénients : préparation de l'étude assez
longue, nécessité de création d'un modèle maillé
à partir du modèle CAO, peu adapté aux toutes
petites pièces, ou aux pièces de forte épaisseur.
Dans la gamme VISI-Flow, il existe un module
travaillant à partir de la "fibre neutre" : faBest.
Le programme utilise des éléments finis quadrangulaires.
Simulation directe sur modèle 3D
Depuis quelques années, une amélioration technique
importante est apparue pour éviter les phases assez fastidieuses
de préparation de la fibre neutre et de maillage. Le modèle
est constitué d'un maillage triangulaire type STL généré
à partir de la géométrie 3D de la pièce,
l'enveloppe de la pièce. Visuellement la pièce apparait
en 3D comme en CAO, mais les calculs restent basés sur
une technologie 2.5D.
Capable de simuler pratiquement n'importe quel type de pièce,
cette technologie élimine les inconvénients de la
technique "fibre neutre" . Il est possible de faire
de petites modifications sur la pièces (changement d'épaisseur,
canaux préférentiels) sans repasser par la CAO.
VISI-Flow utilise
une technique brevetée, associant maillage triangulaire
de surface et maillage hexaédrique du volume de la pièce.
Cette technologie permet une préparation quasi automatique
du modèle et des temps de calcul très courts, sans
réduire la qualité des résultats.
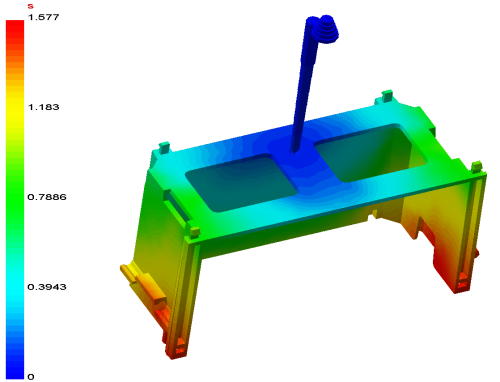
Logiciels "3D" solides. Simulation
volumique
Ces logiciels utilisent aussi des éléments finis, mais dans ce
cas le maillage se fait dans tout le volume de la pièce. Cette
méthode est bien adaptée à l'étude de pièces dans lesquelles la
peau moyenne ou fibre neutre est difficile à définir : petites
pièces, pièces avec de fortes variations d'épaisseur. Les résultats
sont visualisés sous forme de cartes en couleur comme pour le
maillage fibre neutre.
Avantages : Maillage entièrement automatique ne nécessitant
plus de préparation CAO. Représentation fidèle de la géométrie
de la pièce. Adapté à l'étude de pièces complexes. Permet de
prendre ne compte des phénomènes 3D locaux.
Inconvénients : Calculs plus longs (plusieurs dizaines
de minutes à plusieurs heures), modifications de la géométrie
pièce difficiles, peu adapté aux grandes pièces
d'épaisseur constante.
|
|